Carbon-fibre-reinforced semi-crystalline technopolymer guarantees excellent resistance to corrosion even in saline environments. This material’s composition makes the fixtures resistant to impact and sub-zero temperatures at the same time as having a thermal conductivity similar to that of stainless steel. The technopolymer’s high heat dissipation capability means the power supply unit can be housed inside the fixture.
Crafting light for life
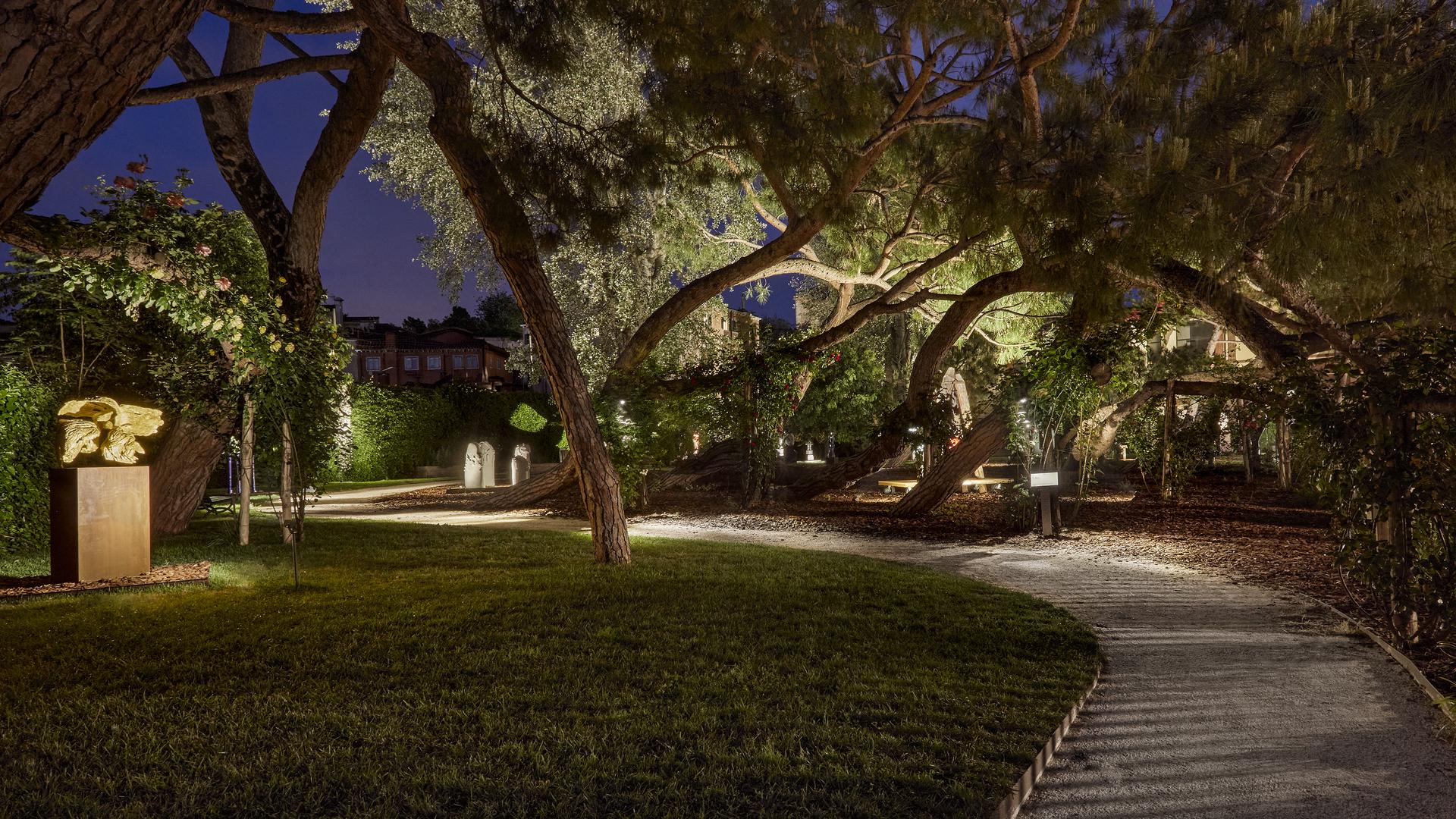
Our company
Born in the future
It all began in Vicenza in 2007 with an ambitious idea: to apply LED technology to the architectural lighting sector and produce high-quality fixtures entirely made in Italy. Luce&Light was founded by Marco Celsan, Alfio Parise and Patrizia Framarin, who all came from the world of technical lighting. LED technology, as we know it today, was still in its infancy, and its adoption was far less widespread than that of other light sources used at the time. Within a few years, LEDs revolutionised the lighting sector, both technically and aesthetically. Curiosity and a passion for technology are still the driving forces behind our company, whose pioneering spirit has pushed it to develop expertise in electronics, mechanics, optics, and materials science. Another reason why our solutions illuminate projects by the most important international architects and lighting designers.
Our plus points
-
Design and production Made in Italy
-
20 years of LED lighting
-
Constant research and development
-
Mechanical, resistance and photometric tests
-
Custom solutions
-
Speedy, prompt delivery
Our Know-how
An LED-native company
We came into being with specific expertise in semiconductors, and, thanks to our combined technical and design skills, we saw the potential of LEDs to transform light. Over time, this expertise has consolidated into a mission to illuminate and enhance architectural spaces with innovative, high-quality solutions, the fruits of advanced technology and a responsible ethos. Thanks to an in-house team of highly qualified designers and technicians, we follow every phase of the process, from design and prototyping to testing and full batch production. Innovation abounds in every detail: in our patented protection systems; our selection of LEDs and materials; and the design of optics, such as our very narrow 2°. But, above all, innovation is constantly present in every process, like the technological developments we have learnt to keep pace with.
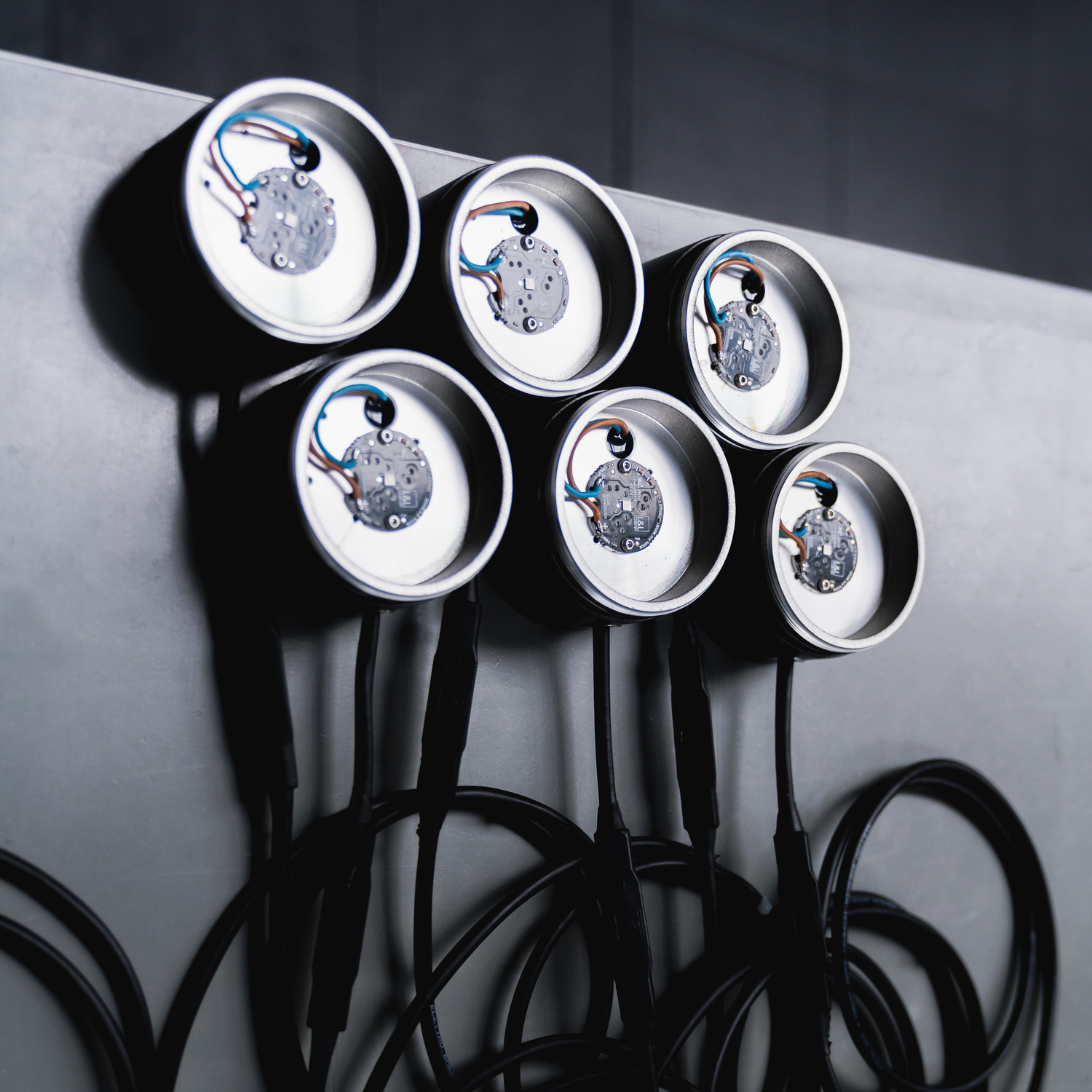
Technical design
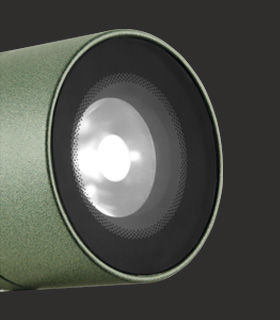
This involves not only the design and study of lighting performance but also the careful research and selection of LEDs and raw materials, an essential part of ensuring our products’ high quality and long-term reliability.
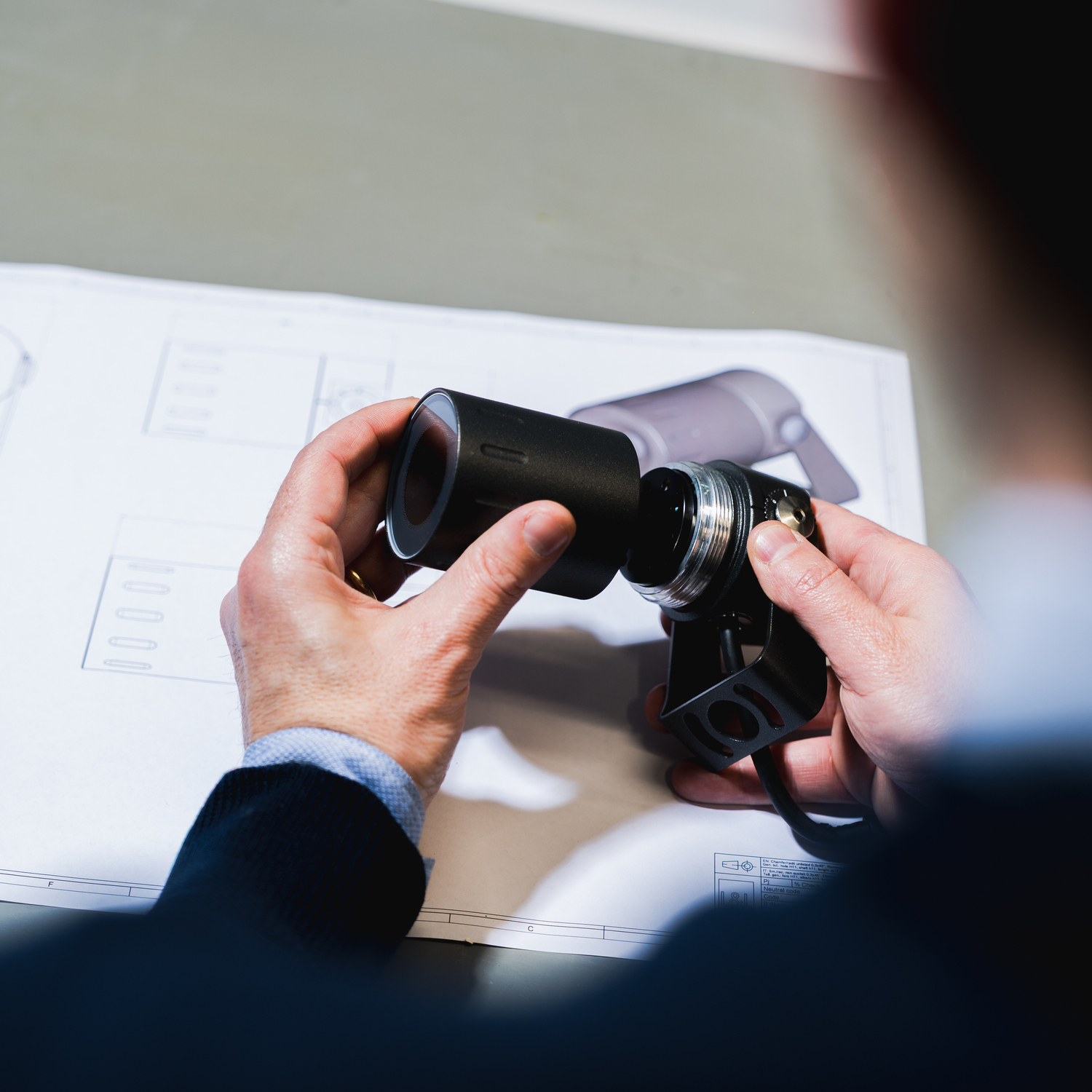
Research and development laboratories
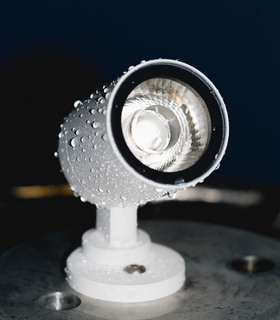
All the lighting fixtures under development undergo scrupulous photometric, mechanical, thermal and resistance tests in our laboratories.
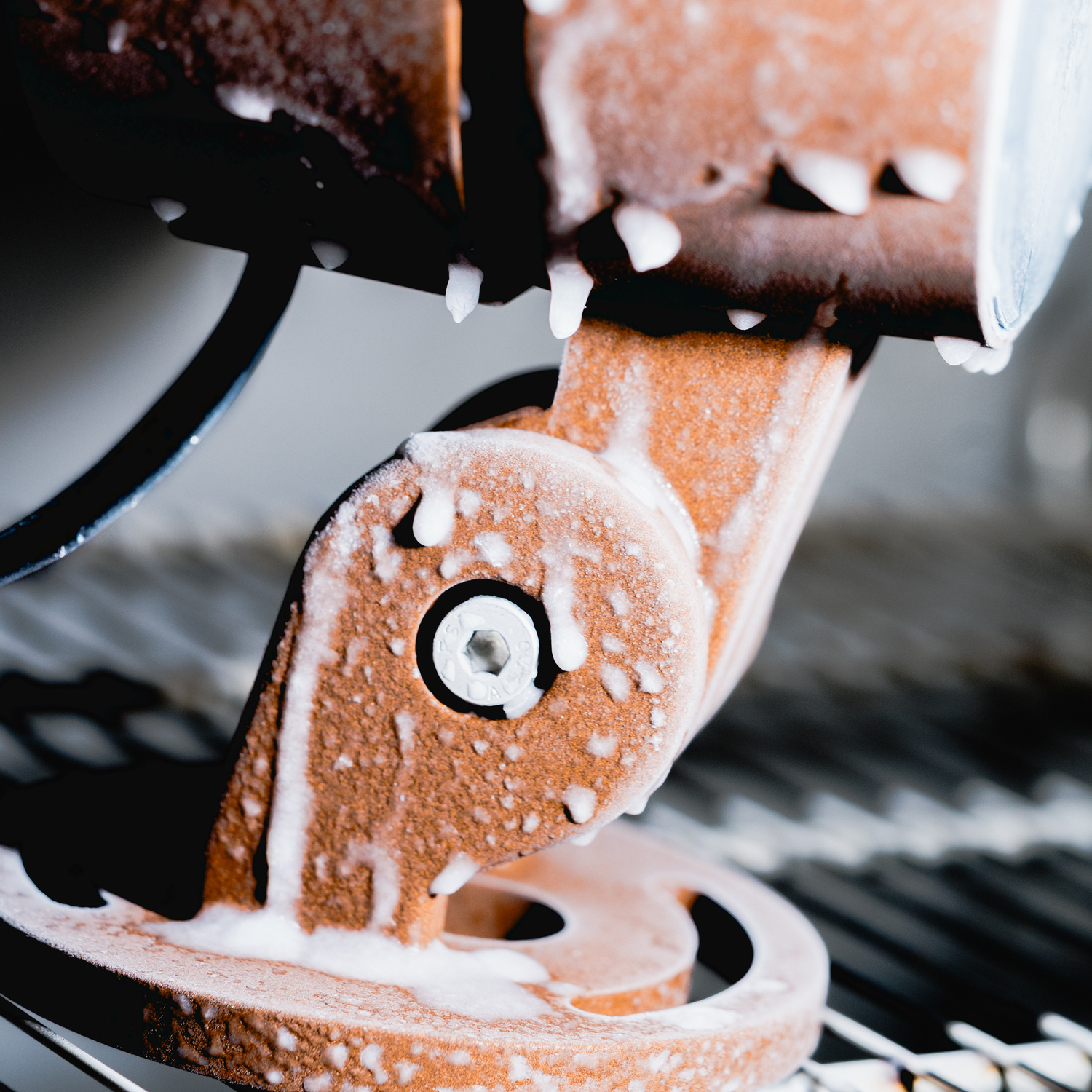
In-house production
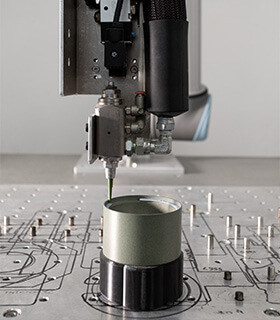
Our in-house mechanical and electronic production cycle in Vicenza allows us to maintain a high level of quality and meet delivery times, and to readily satisfy the demand for customized solutions.
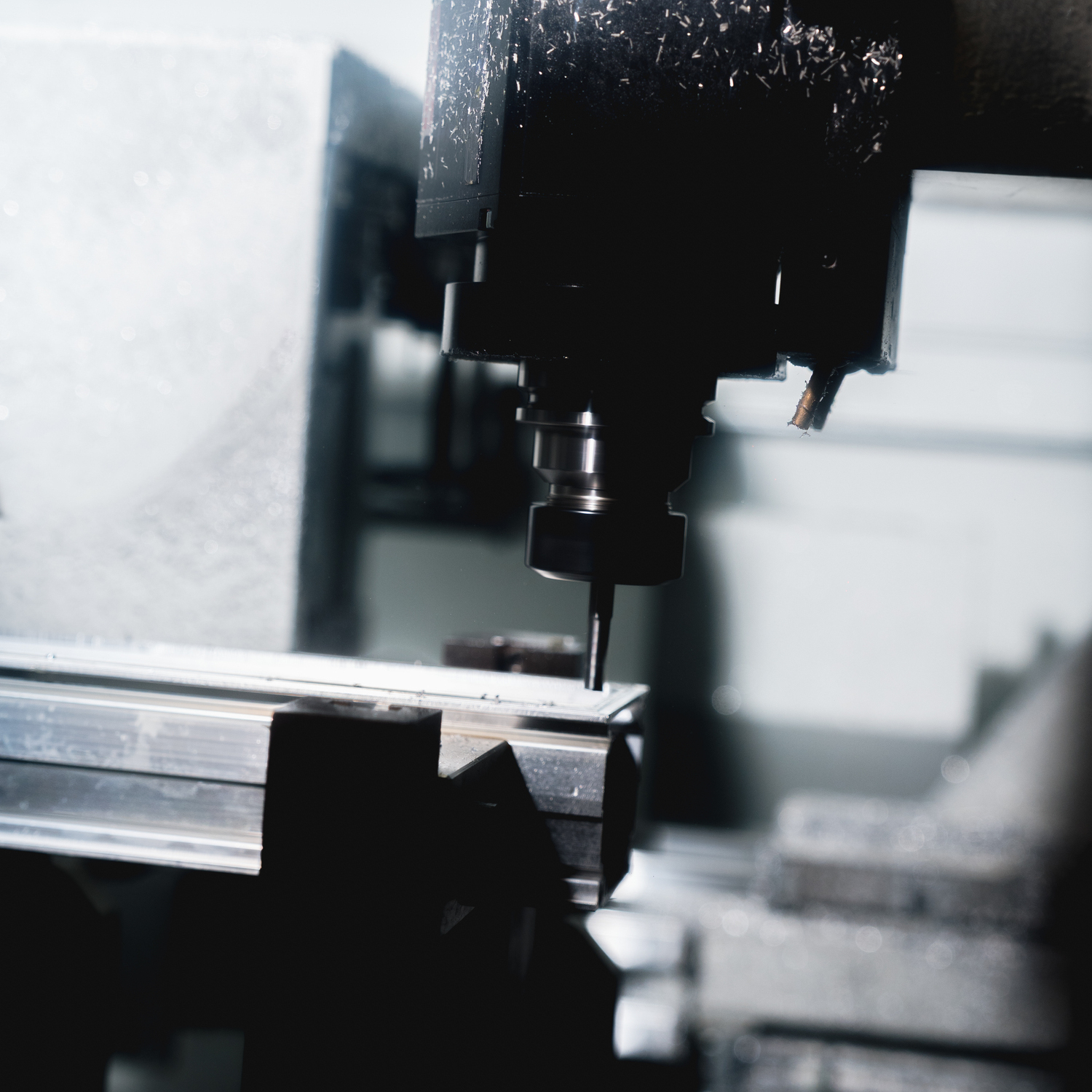
End of line testing on all fixtures before shipment

All our lighting fixtures are tested and approved with EoL (End of Line) testing, with function tests and power-consumption parameter checks.
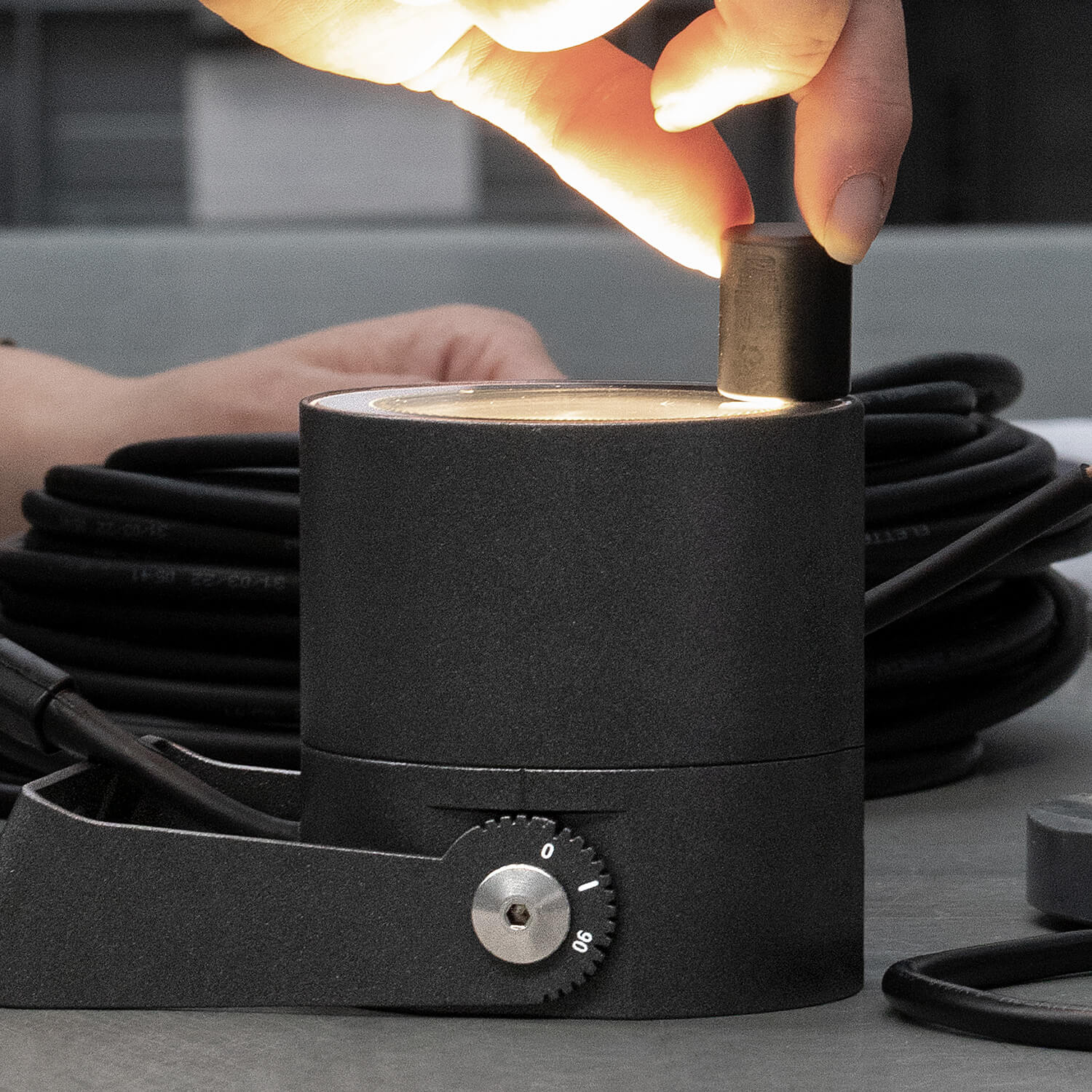
Pre- and post-sales services
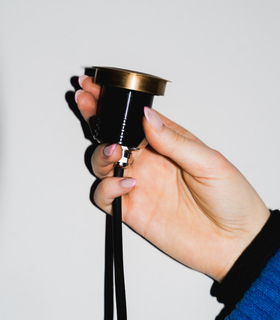
We provide exceptional support to all our customers in the sales and after-sales stages through our international customer care team. Our attentiveness and willingness to help also enable us to suggest customized solutions.
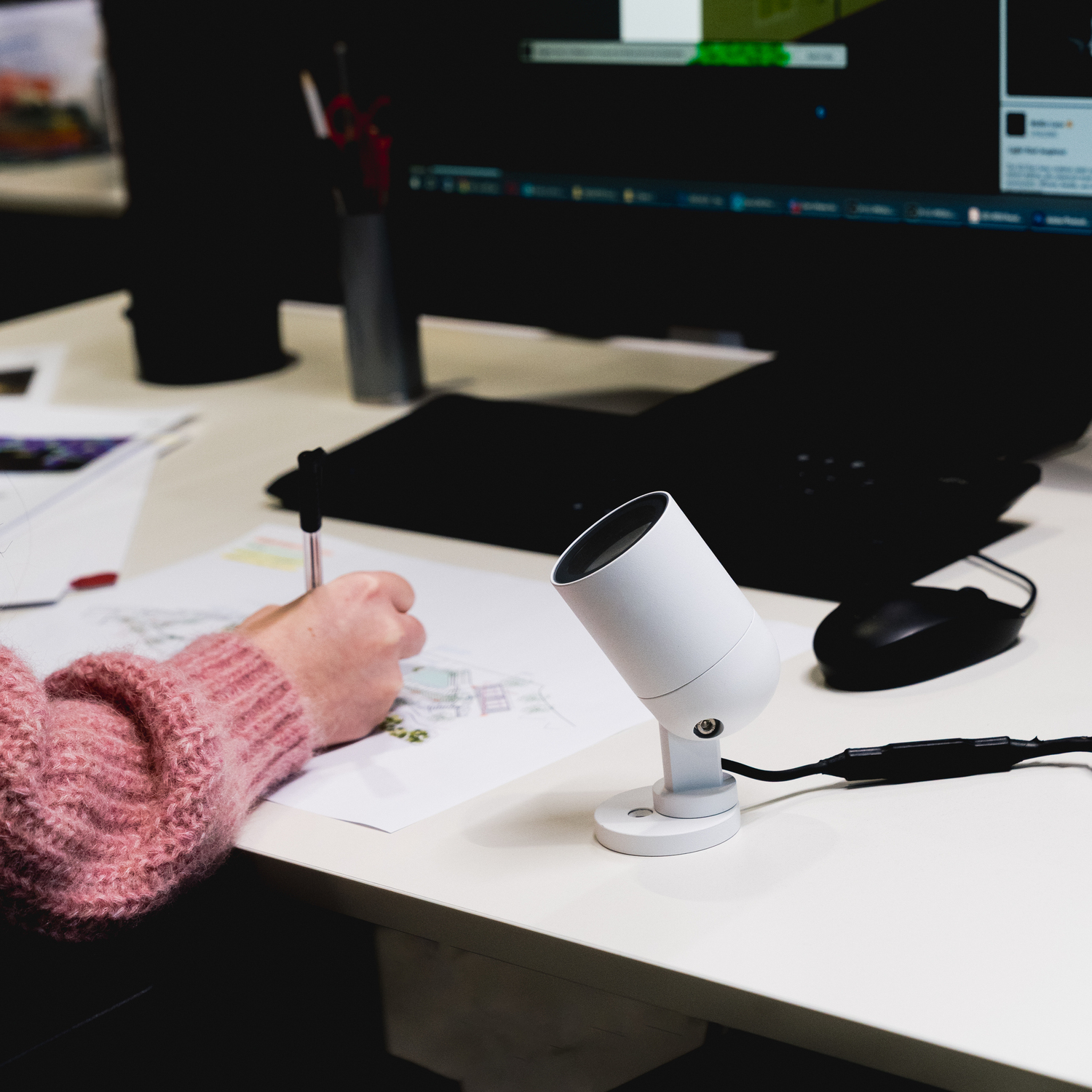
Our technical processes
Quality that stands the test of time
Careful material choices and meticulous painting processes ensure that the function and appearance of our lighting fixtures remain unchanged, even when exposed to adverse atmospheric and environmental conditions.
-
Technopolymer
-
Glass
-
AISI 316L stainless steel
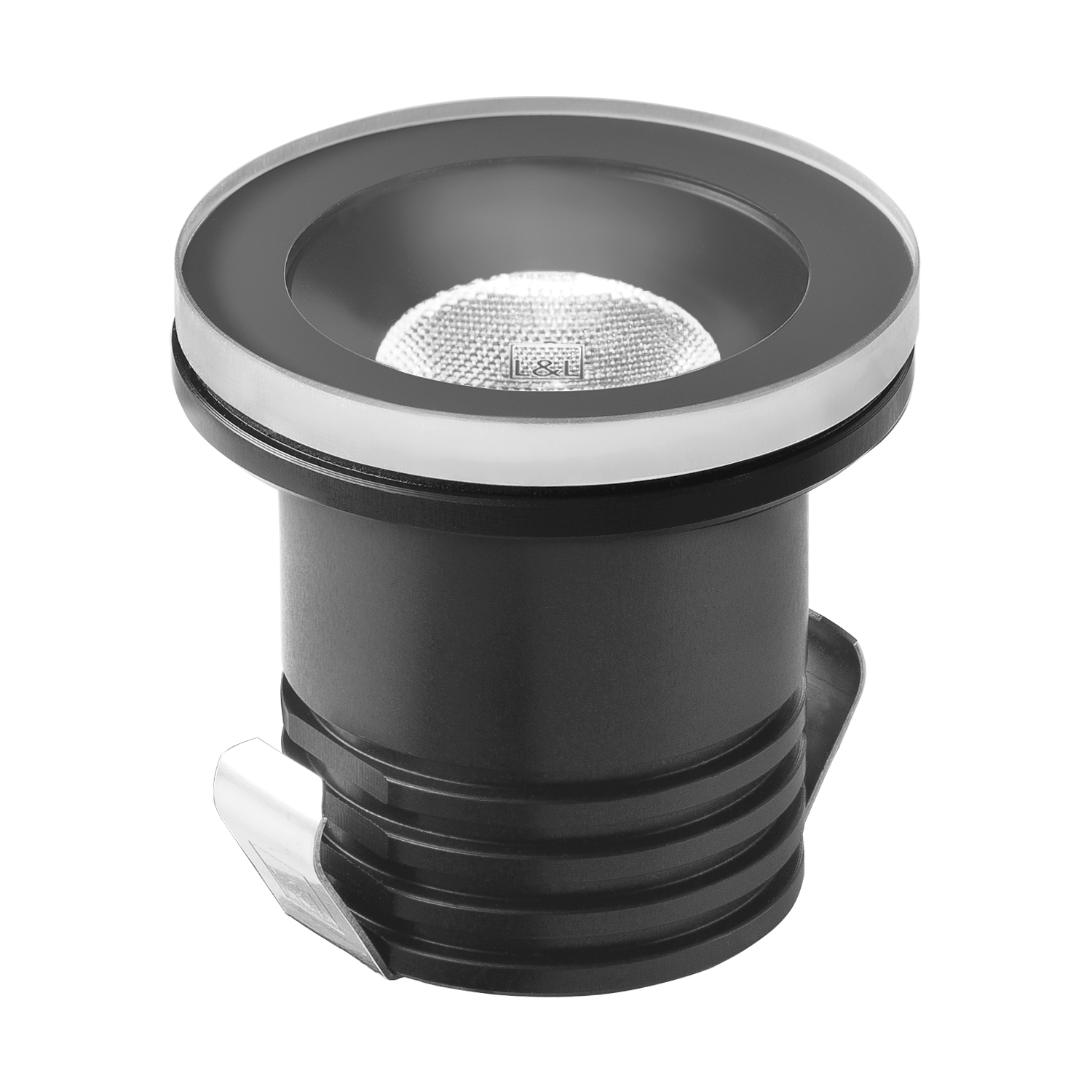
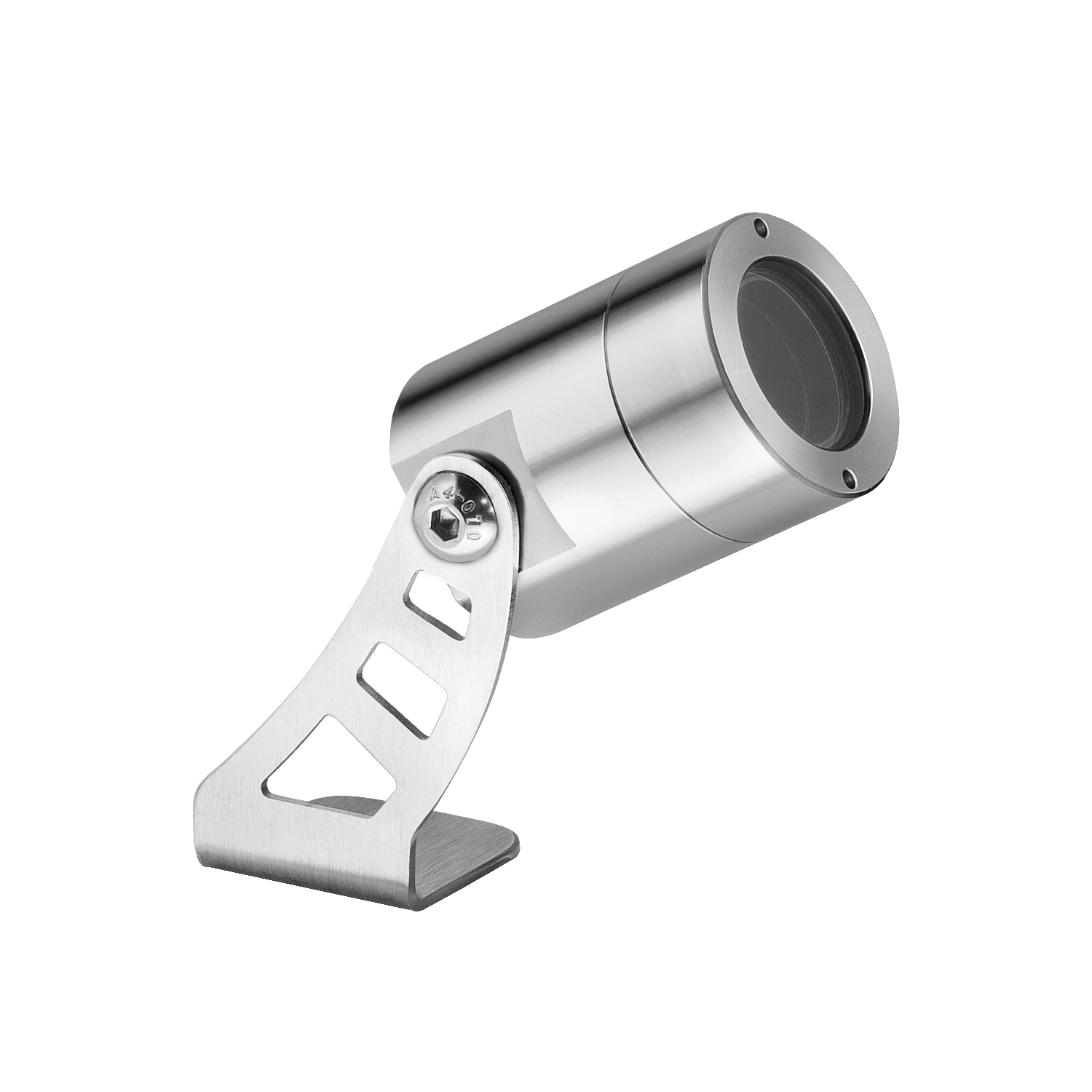
-
Surface preparation
Conversion coating with ceramic nanoparticles, which increases corrosion resistance and improves paint adhesion.
-
Epoxy paint
-
Polyester paint
-
Salt-spray testing
-
Paint thickness testing
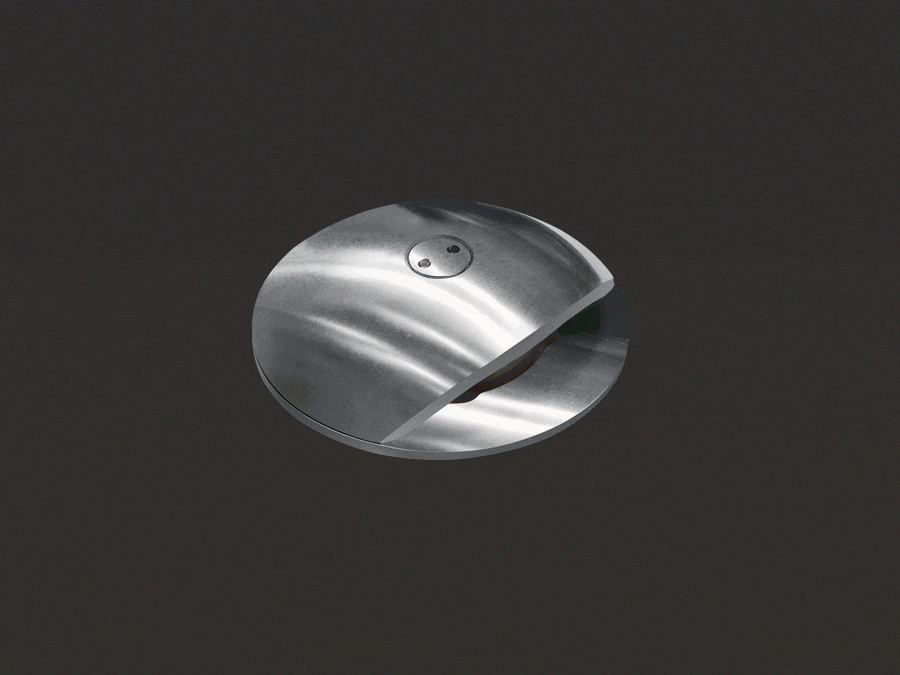
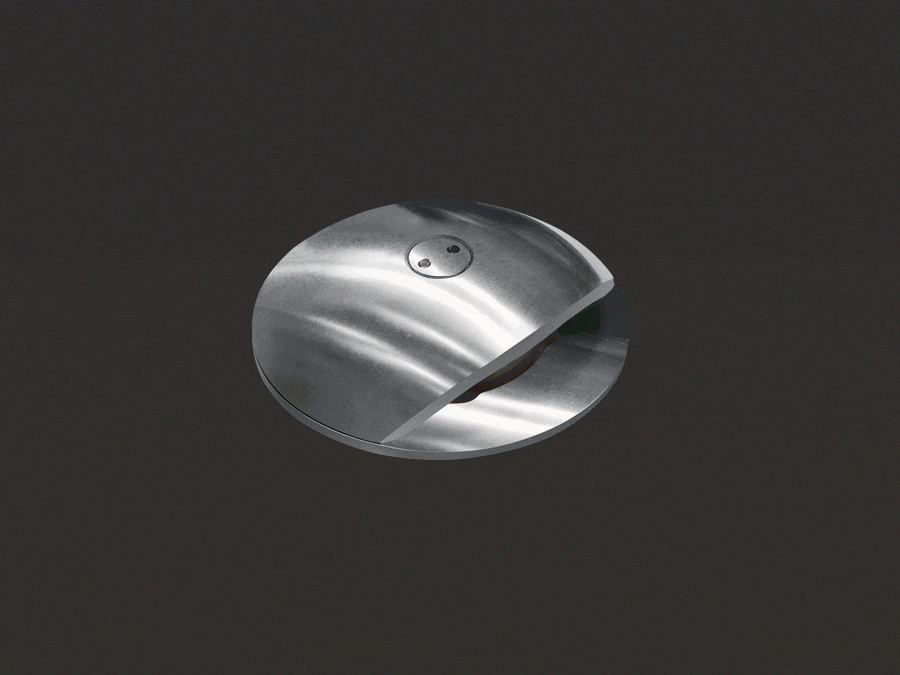
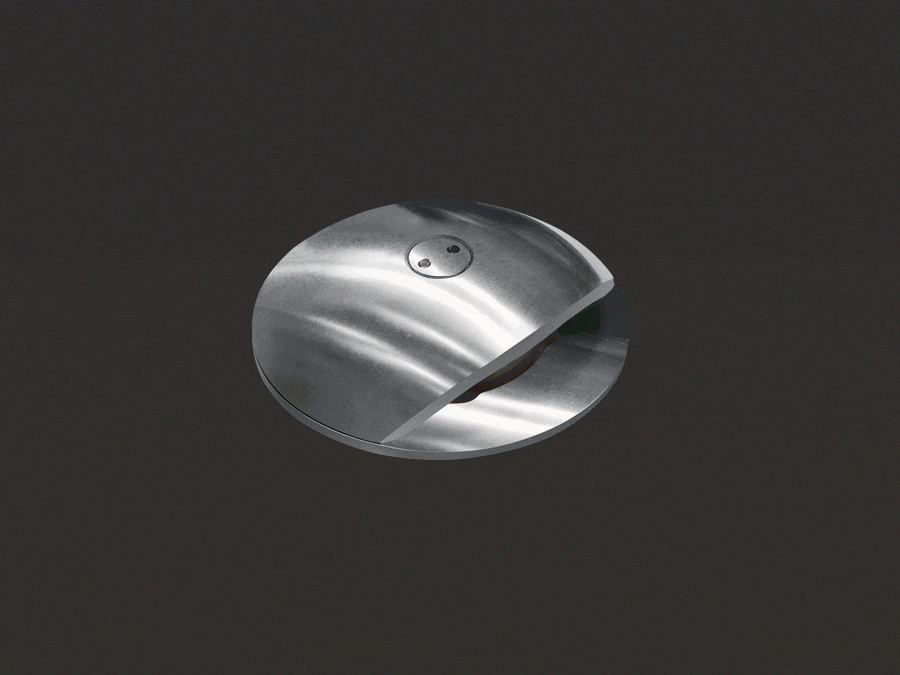
-
Electrical protection system
Protects indoor fixtures against electrical problems.
This patented L&L innovation guarantees electrical protection against polarity reversal, hot plugging and voltage spikes of up to 48Vdc, which can occur if there are faults in the electrical circuit. -
Intelligent protection system
-
Protective Impedance Device
-
Surge Protection Device
-
Temperature control built in (NTC)
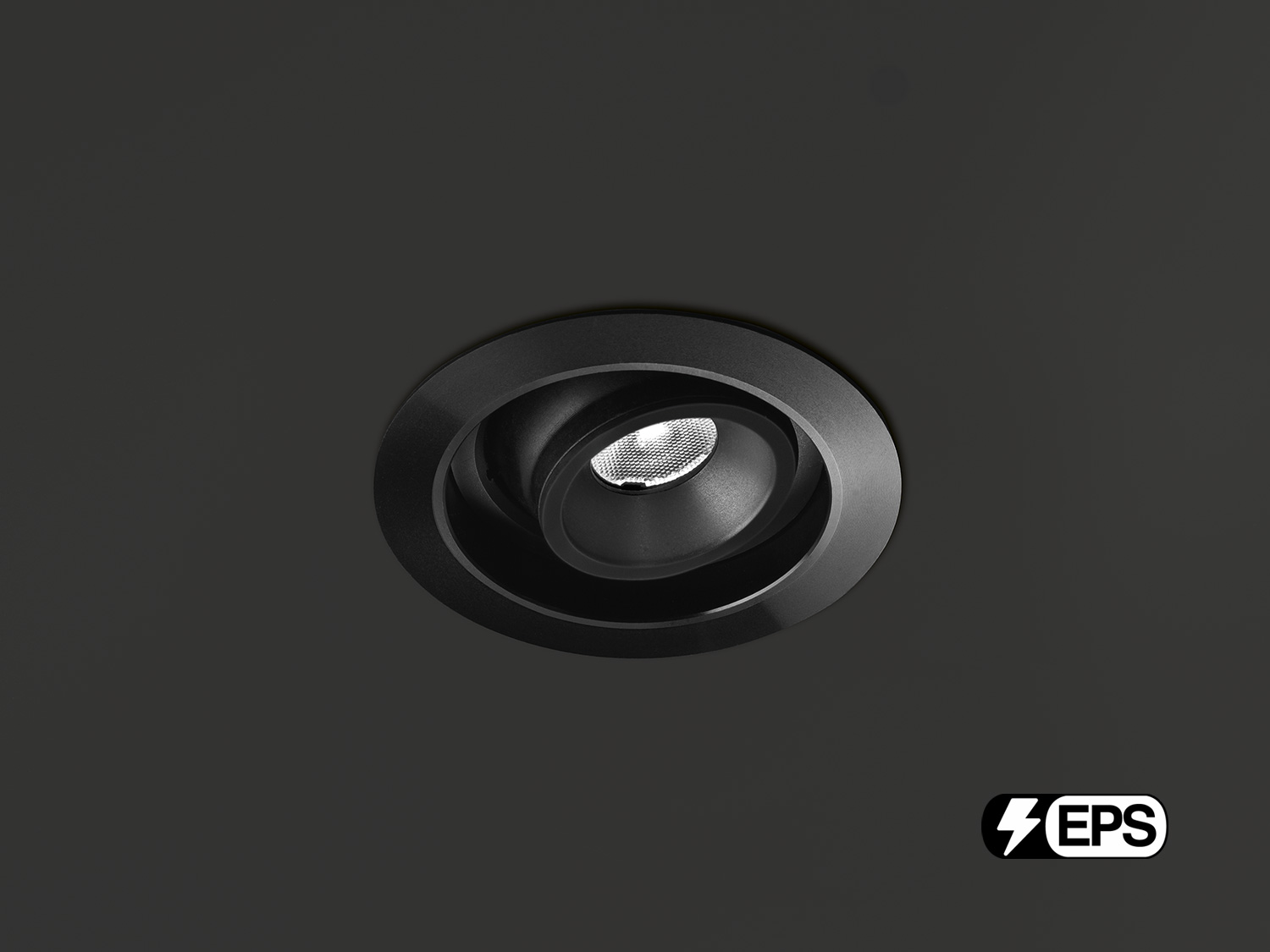
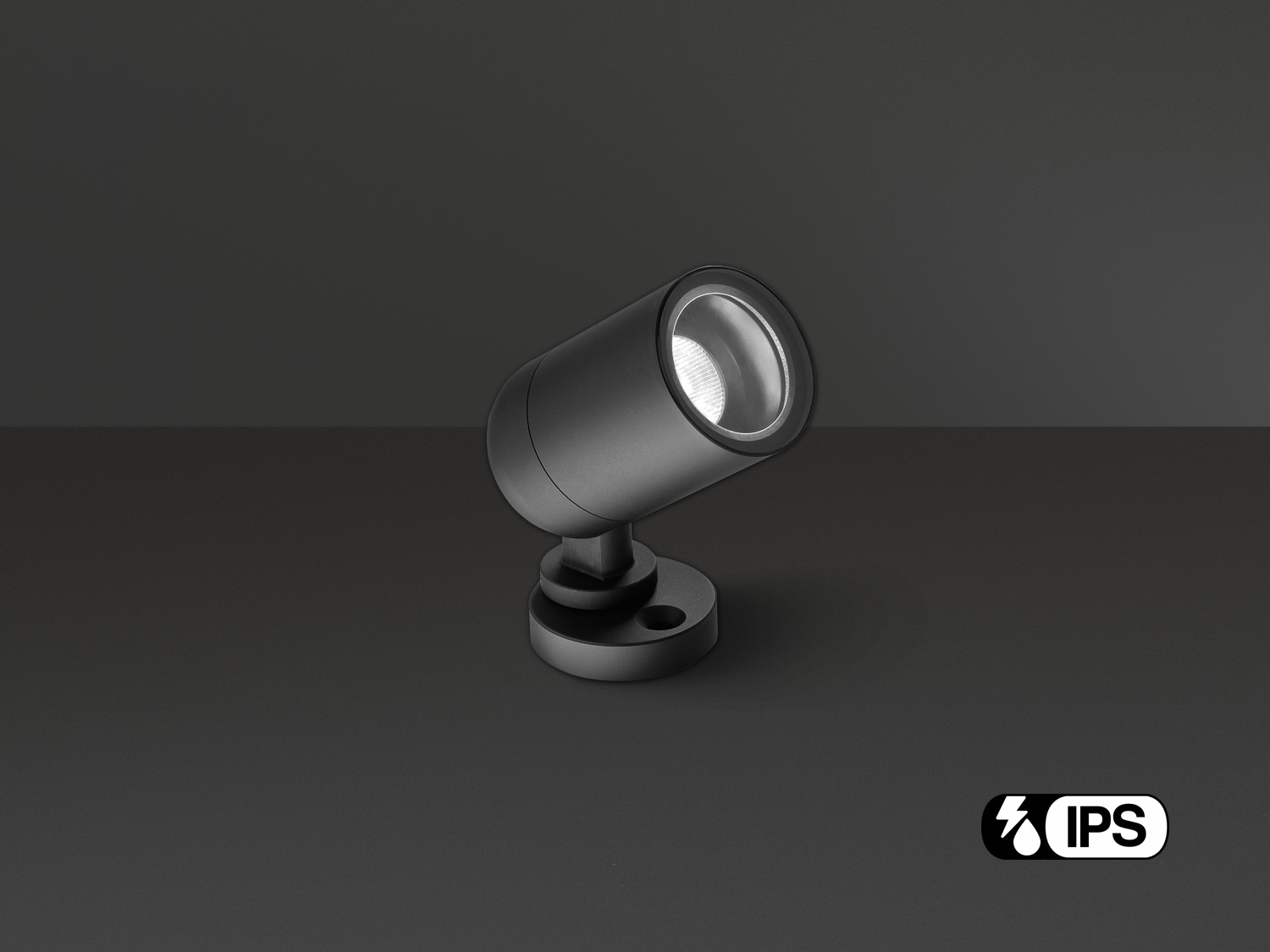
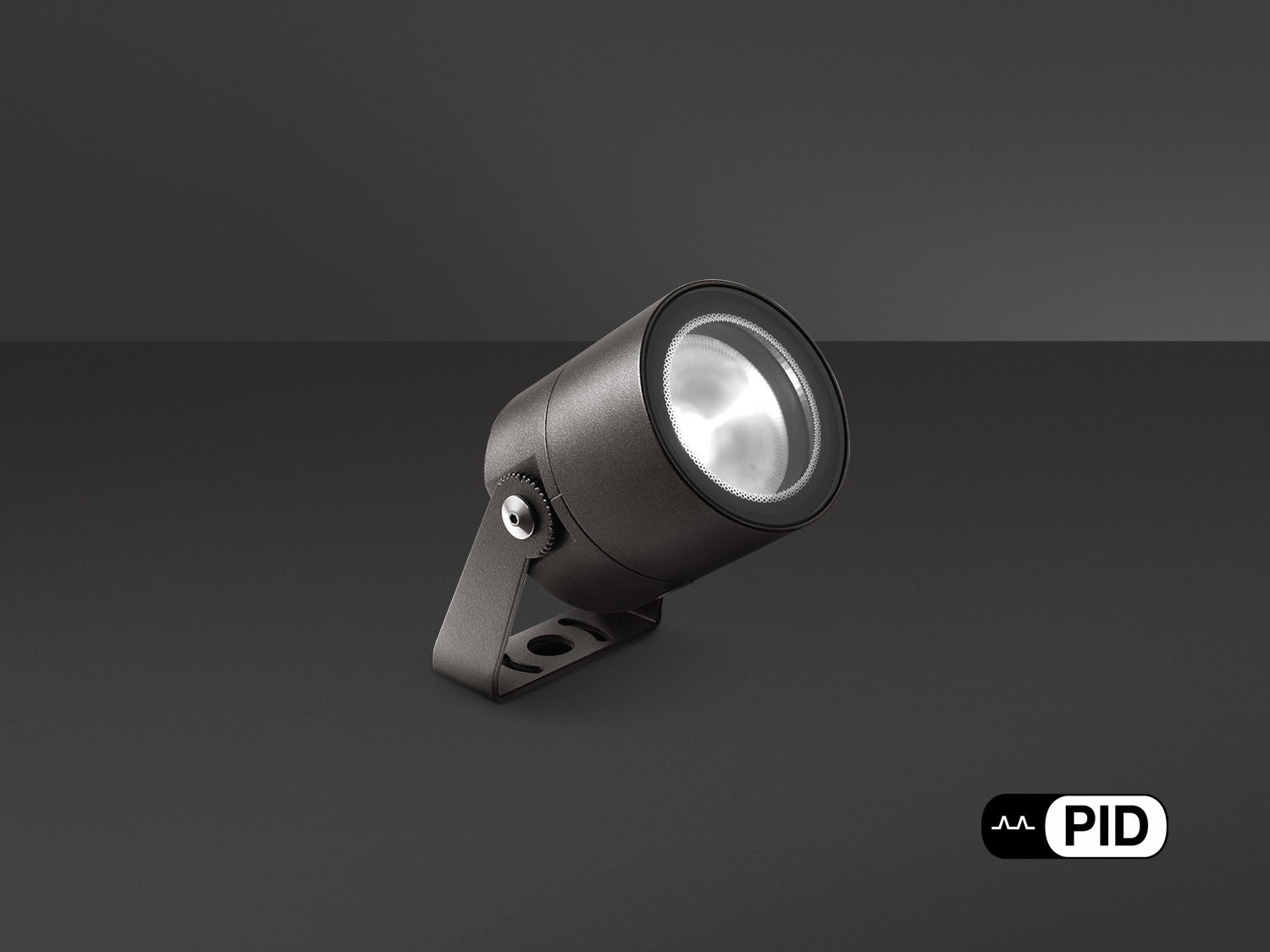
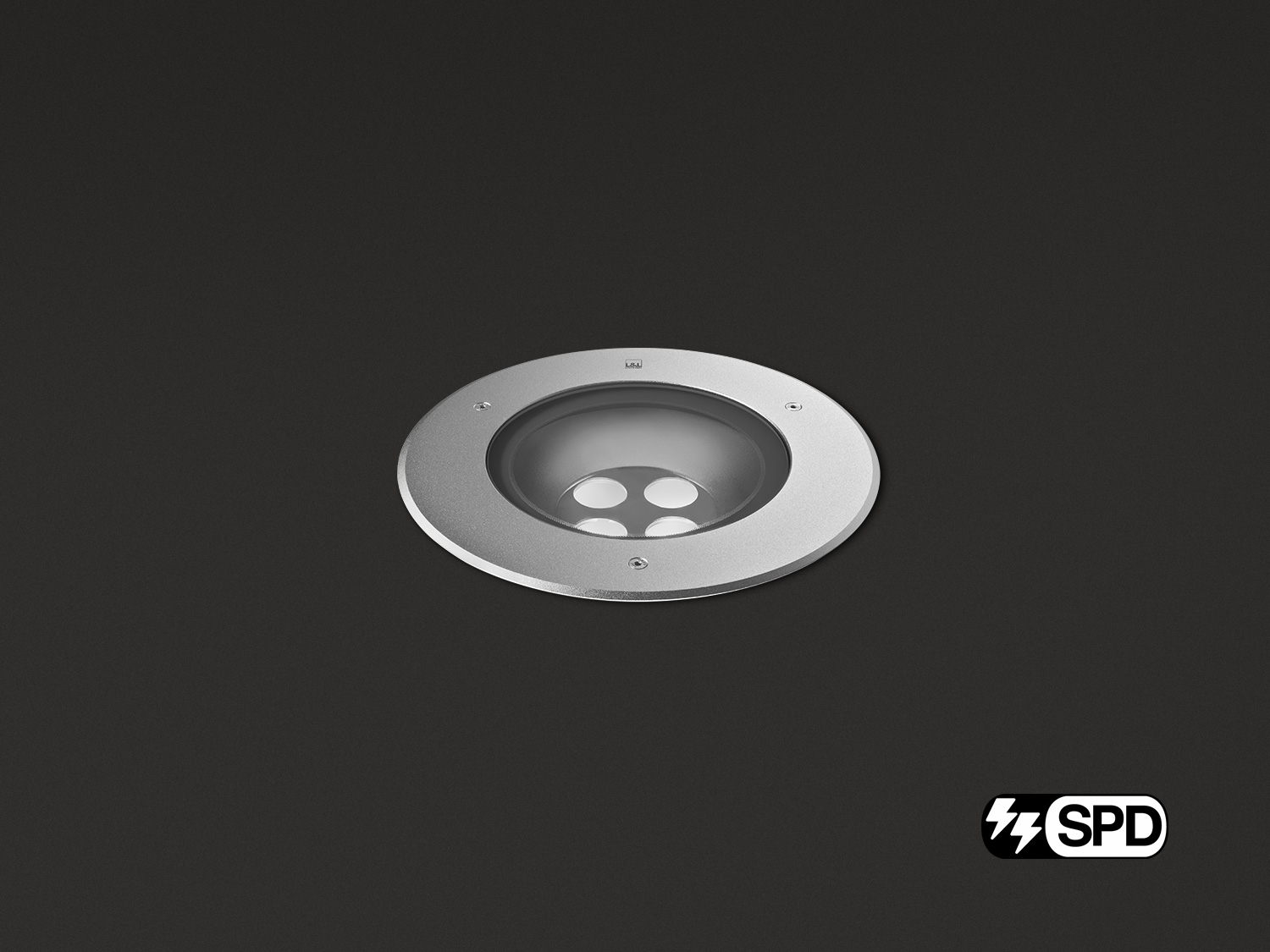
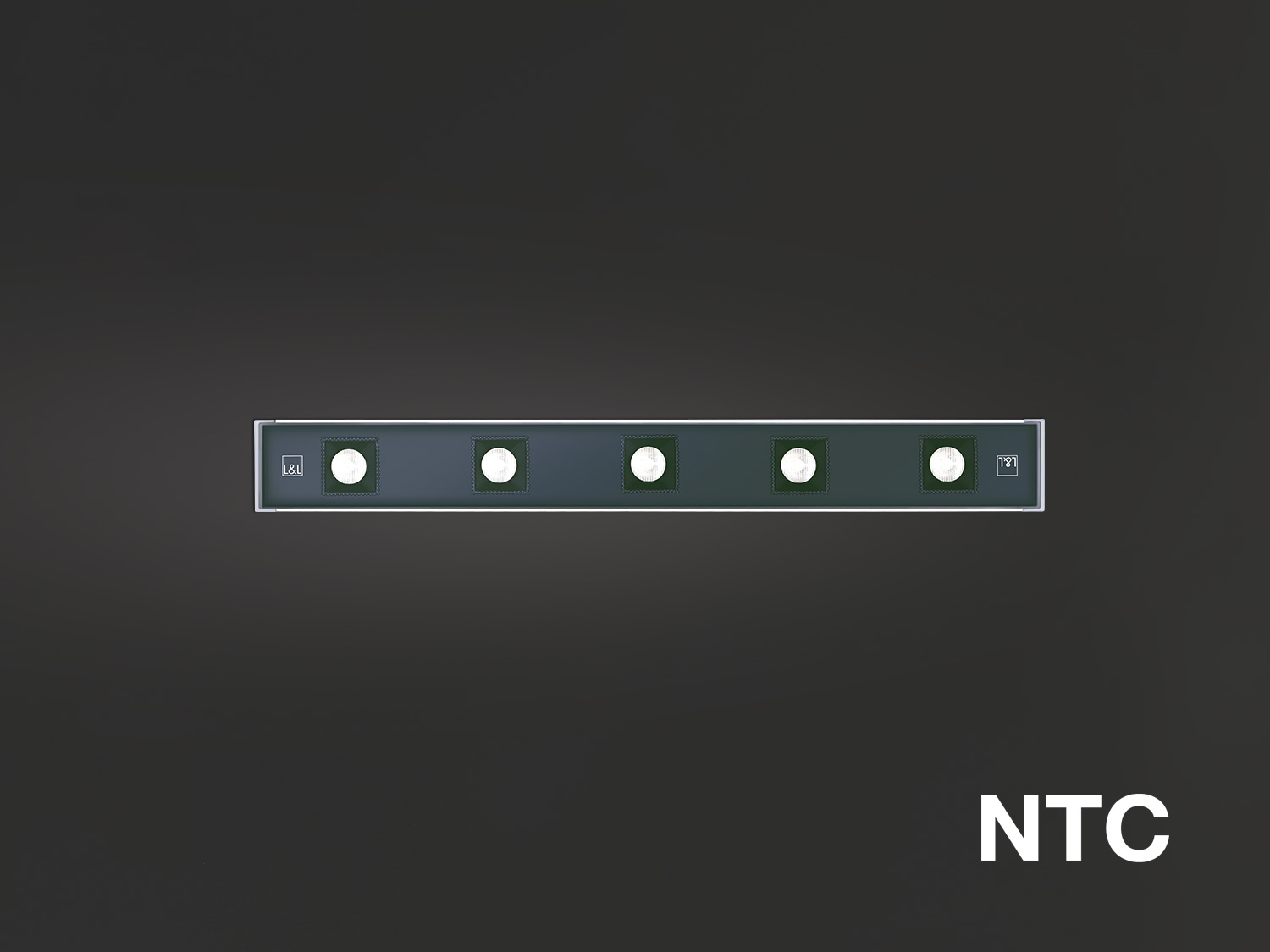
Why you can trust L&L
Our company is certified to ISO 9001, the international standard that assesses corporate quality management systems. In addition, we have the necessary product conformity certification for the sale and export of lighting fixtures to specific markets or countries.
Find out more